PRODUCT OVERVIEW
Electric eccentric hemispherical valve is a product composed of eccentric hemispherical valve and electric actuator. The product has the advantages of small opening force, stable performance, good sealing, compact structure and so on. The eccentric hemispherical valve uses the eccentric valve body, eccentric ball and valve seat. When the valve rod rotates, it is automatically centered on the common track. The more it is closed, the tighter it is in the closing process, so as to fully achieve the purpose of good sealing. The ball of the valve is completely separated from the valve seat, which eliminates the wear of the sealing ring and overcomes the problem that the traditional ball valve seat and the sealing surface of the ball are always worn. It is suitable for sewage, papermaking, petrochemical industry, natural gas medium, granular fluid and powder solid, especially for steel, aluminum, papermaking, petroleum, metallurgy and other industries.
PRODUCT ADVANTAGES
1. Solve the problem of poor valve sealing caused by precipitation and easy scaling of particles, powder, pulp and other media in metallurgy and paper industry.
2. The switch is light, the ball is separated from the shell when opening without any contact, the starting torque is small and the rotation is flexible. When closed, the squeeze cutting action between the hemisphere and the valve seat can remove the dirt on the sealing surface, so that the valve can be opened and closed smoothly, with high safety factor and good sealing performance.
3. The eccentric structure of the sealing surface can automatically compensate the wear of the spherical surface, ensure the sealing performance of the valve, and 100% will not leak. Using this valve to control the pipeline has high safety performance.
4. This valve is electrically driven, which is very convenient. You can also select the appropriate torque and brand electric actuator according to the customer's working conditions. Remote control can also be selected according to the requirements of working conditions.
MATERIAL OF MAIN PARTS
Serial number | Part name | Material name |
1 | Body / bonnet | WCB | ZG1Cr18Ni9Ti | ZG0Cr18Ni12Mo2Ti | ZG15Cr1Mo1V |
2 | sphere | WCB+Hard chromium | 1Cr18Ni9Ti Special surface treatment | 0Cr18Ni12Mo2Ti Special surface treatment | 25Cr2Mo1V Special surface treatment |
3 | Valve stem | 20Cr13 | 1Cr18Ni9Ti | 0Cr18Ni12Mo2Ti | 25Cr2Mo1V |
4 | valve seat | Q235A+PTFE/Surfacing | 1Cr18Ni9Ti/PTFE | 0Cr18Ni12Mo2Ti/PTFE | 25Cr2Mo1V/PTFE |
5 | filler | Flexible graphite | Flexible graphite | Flexible graphite | Flexible graphite |
6 | Bolt | 35CrmoA | 0Cr18Ni9 | 0Cr18Ni9 | 15Cr1Mo1V |
7 | Nut | 45 | 0Cr18Ni9 | 0Cr18Ni9 | 20CrMo |
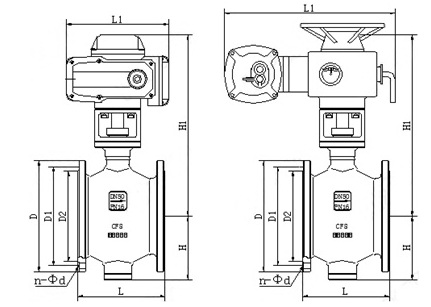
MAIN OUTLINE AND CONNECTION DIMENSIONS
Nominal pressure PN(MPa) | Nominal diameter DN | Dimensions(mm) |
L | D Series 1 / Series 2 | D1 | D2 | D6 | b | f | Z-φd |
mm | in | Flange |
1.0 | 40 | - | 125 | 145 | 110 | 85 | - | 16 | 3 | 4-18 |
50 | - | 140 | 160 | 125 | 100 | - | 16 | 3 | 4-18 |
65 | - | 190 | 180 | 145 | 120 | - | 18 | 3 | 4-18 |
80 | - | 178 | 195 | 160 | 135 | - | 20 | 3 | 4-18 |
100 | - | 200 | 215 | 180 | 155 | - | 20 | 3 | 8-18 |
125 | - | 254 | 245 | 210 | 185 | - | 22 | 3 | 8-18 |
150 | - | 267 | 280 | 240 | 210 | - | 24 | 3 | 8-23 |
200 | - | 292 | 335 | 295 | 265 | - | 24 | 3 | 8-23 |
250 | - | 330 | 390 | 350 | 320 | - | 26 | 3 | 12-23 |
300 | - | 390 | 440 | 400 | 368 | - | 26 | 4 | 12-23 |
350 | - | 430 | 500 | 460 | 428 | - | 28 | 4 | 16-23 |
400 | - | 530 | 565 | 515 | 482 | - | 28 | 4 | 16-25 |
450 | - | 580 | 615 | 565 | 532 | - | 30 | 4 | 20-25 |
500 | - | 630 | 670 | 620 | 585 | - | 30 | 4 | 20-25 |
600 | - | 800 | 480 | 725 | 685 | - | 34 | 5 | 20-30 |
700 | - | 900 | 895 | 840 | 800 | - | 38 | 5 | 24-30 |
800 | - | 1000 | 1010 | 950 | 905 | - | 42 | 5 | 24-34 |